The IT startup has managed to effectively solve an essential problem in the entire transport logistics. Using only one single source the industry and logistics service providers are experiencing a new way of handling their loading requirements, efficiently.
In today’s rapidly evolving digital landscape, small & medium-sized companies as well as large corporations must overcome a wide range of challenges. They need to know how to be successful and stay competitive in the global market. Using software and technologies to automate business processes and functions can become a key factor in order to differentiate own products and services from their competitors.
Different types of information sources are disabling the digitalization in logistics
While other industries keep up with digital transformation of their businesses, logistics is still mainly driven by manual processes. Up to 5% of trucks are rejected due to unclear or unknown requirements.
Shipping companies, logistics service providers and goods consignees are the first ones suffering the consequences. Digital transformation has been the major logistics challenge of the last 10 years. The digitization of the entire supply chain provides logistics partners with the latest digital solutions to fundamentally improve their visibility into operations. For example, using Track & Trace or IoT- and AI apps for freight procurement and freight planning. There are different channels used to communicate data between shippers and carriers. However, for purchase orders, shipping notices, invoices, or any documents to be exchanged still prevail EDI tools, that replaced paper-based documents about 20 years ago. Since decades, logistics runs via phone, email, fax and spreadsheets – a fact that still remains in 2023. The digitalization of the entire B2B logistics is progressing slowly compared to other industries. According to the Economy index DIGITAL logistics ranked only second to last place.
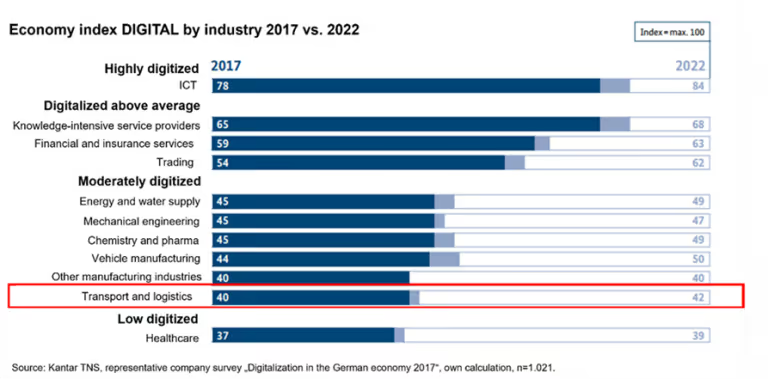
Fig. 1: Economy index DIGITAL 2017 vs. 2022.
One of the key factors that is slowing down the efficiency of transport logistics in terms of successful cooperation, higher reliability and planning capability is a lack of appropriate communication. Contract and transport-relevant (un-)loading requirements are still managed in unstructured freetext fields and communicated inefficiently.
Some examples: a truck arrives during the opening hours of the gate, but too late for unloading at the particular loading point. Required technical or safety equipment is missing. The carrier hasn’t brought a suitable pump or simply some documents necessary for receiving products are incomplete. The reason for these defects to happen is simple: inaccurate or obsolete information. All parties – shippers and carriers – are trying to keep up with the relevant requirements in their own way. There is no clear data and no clear communication. Consequently, troubleshooting and never-ending discussions about truck specifications, local procedures and other restrictions occur daily. Generally, logistics partners make use of what they know and not of what is sent, because they don’t trust the information. That means, that in the worst case they have received updated requirements, but do not believe they are valid. At the end of the day all parties involved are faced with continuously rising costs, more delays, frustration, extra and empty kilometers. This is exactly why we have developed Loady and built together with logistics experts a platform that makes (un-)loading processes cost-efficient and sustainable.
A standardized platform for (un-)loading requirements finally enables transparent logistics
Loady optimizes the entire B2B transportation process: from freight procurement, freight ordering, transportation planning and dispatching, to actual delivery. Companies maintain directly in Loady the requirements to be followed for loading their sales products or unloading the products delivered to them at their sites. By means of temporarily limited assignments, they share the information necessary for the operational process with their business and logistics partners.
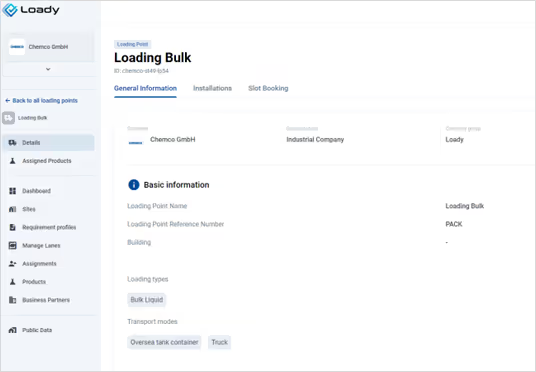
Fig. 2: Maintaining requirements in Loady, here: access restrictions for loading bulk products
Loady simplifies the requirements’ management also for logistics service providers. Companies are providing their partners with valid information on (un-)loading requirements, informing automatically about any process changes. Doing logistics this way makes all parties involved happy, because misunderstandings don’t arise at all. This translates directly in less truck rejections, less delays and troubleshooting, increased planning capability and an easier life for the drivers
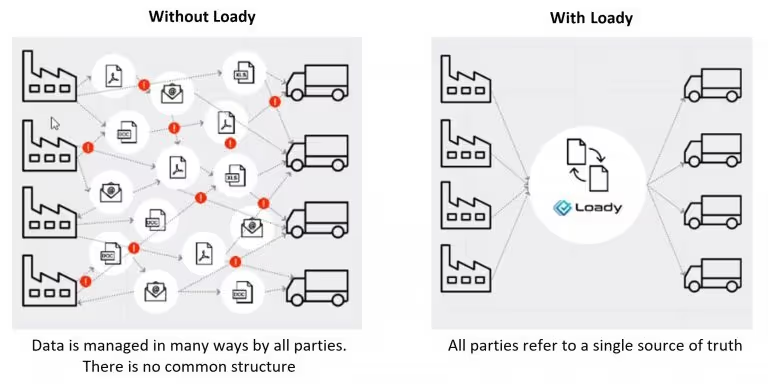
Fig. 3: Handling loading and unloading requirements in the logistics, with and without Loady
With Loady, relevant and updated (un-)loading requirements are always available. The standardized platform offers different modules according to the different customers’ needs. An intuitive user interface and a clear structure support them in handling their data efficiently – decreasing costs and increasing efficiency. With Loady API, companies can integrate master data from their systems to Loady, enrich the data there with additional attributes – e.g. pre-product or site logistics specifications – and then get a full, up-to-date data set automatically back to their systems for further processing. Today Loady is available in different European languages – German, English, Polish and Spanish. Loady keeps growing and therefore will be introducing in future another languages as well.
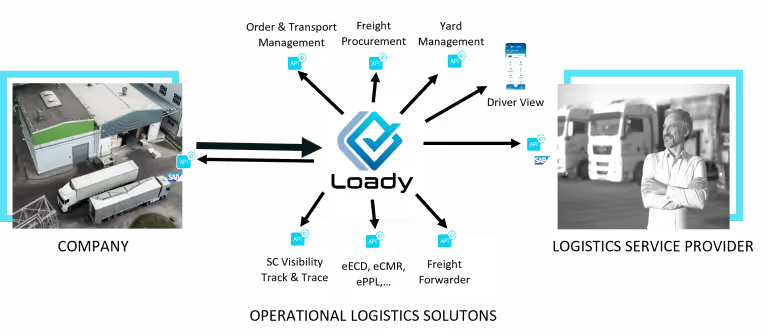
Fig. 4: Reliable and up-to-date loading requirements used in processes are available on the interoperable platform Loady
Via mobile view Loady2Go, drivers can access updated (un-)loading requirements in a comprehensive way and switch the language with one click. This makes it much easier to manage deliveries even to new places and prevents unnecessary waiting times and (un-) loading incidents.
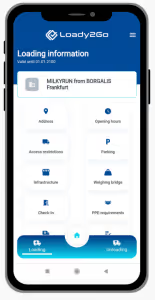
Fig. 5: Multilingual Driver View Loady2Go
The vision behind Loady is simple: we want to help companies and carriers all over the world to improve their logistics processes by communicating clear information more efficiently along the supply chain.
A Venture of BASF is becoming the industry-wide standard for logistics data
Loady is a venture of Chemovator GmbH, the business incubator of BASF. After first conversations and workshops with internal and external experts in logistics and chemical transportation, the idea of a centralized platform and place to go for valid information was born. “We would have never imagined that there were still so many manual processes, break and pain points in logistics processes,” so Stefanie Kraus and Elzbieta Wiankowska – both co-founders of Loady and former employees of BASF SE. Despite digitalization, master data used in logistics is managed the same ways for the last 25 years. In 2021 they pitched their idea of Loady at Chemovator, the business incubator of BASF. The jury noticed immediately the potential of Loady and the impact that such a platform would have on the entire industry. So, they started to build the solution.
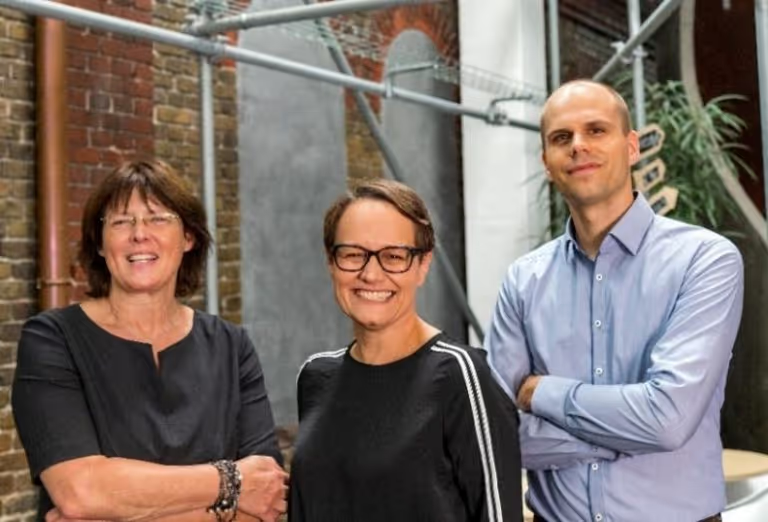
Fig. 6: Co-founders of Loady Stefanie Kraus (CEO), Elzbieta Wiankowska (COO) and Dennis Jantos (CTO)
During the pilot phase in 2022, BASF and Evonik were the first industrial companies to test Loady with several bulk and packed product transports. Also logistics service companies like Bertschi, Lanfer and Talke participated in the pilot. Meanwhile, more than 20 European industrial sites, 30 (un-)loading points and 150 products to be transported are onboarded. In September 2023, Loady will spin off as an own company.
An innovative approach developed for the chemical industry is about to become an industry-wide, standardized, digital platform for logistics, globally.
About Loady
Loady is an industry partner platform that enables an effective and seamless communication of loading and unloading requirements along the supply chain network: from logistics procurement to freight order management, planning and dispatching, up to the physical delivery of goods.
In Loady, companies can maintain their site and product specific specifications in a standardized data structure, and then share them with their business partners and carriers in a secure way. Loady provides a multilingual driver’s view, but companies can also connect to their systems and bring up-to-date requirements directly into the specific operations and processes.
Loady improves the overall supply chain collaboration, helps to avoid truck rejections, and makes transportation services more efficient, reliable and sustainable. Loady is key success factor to further digitization and automation in logistics.
Loady (loady.com) is a venture of Chemovator GmbH, the business incubator of BASF
Email: info@loady.com
Web: www.loady.com